Coker Cranes for Harsh Environments: High Temperature and Corrosion Resistant Design
In a coking plant, the coker crane is responsible for removing the newly produced high-temperature coke from the coke pit to allow the material to cool. After approximately 24 hours, once the coke has cooled and excess moisture has been removed, the crane transfers it to the crusher, hopper, or conveying system.
- Lifting Capacity: 5-20T
- Span: 10.5-31.5m
- Lifting height: 8-26m
- Work duty: A6-A8
- Power Source: 380V/50Hz/3Ph
- Control Mode: Floor control / Remote control / Cabin room control
- Price: Customized Pricing
Coker Overhead Crane Features
- Extreme environmental adaptability: Capable of stable operation in environments with high temperature, high humidity, corrosive gases (H₂S/SO₂), and abrasive dust.
- All-weather high-efficiency operation: Ensures seamless connection throughout the coke handling process, avoiding production interruptions.
- High-temperature coke handling: Capable of directly grabbing coke at temperatures above 500°C, enhancing operational safety and efficiency.
DGCRANE Enclosed Unmanned Coke Removal Crane System
The standard configuration includes: grab bucket bridge crane + intelligent crane management system + smart remote control console + 360-degree monitoring system.
The DGCRANE enclosed unmanned coke removal crane system features fully automated operations such as fixed-point grabbing, yard transfer, unloading, and loading. The system enables precise remote control, preventing operators from being exposed to high-temperature, high-humidity, and toxic environments. At the same time, it enhances the efficiency of crane operations, achieving safe, efficient, and unmanned coke removal.
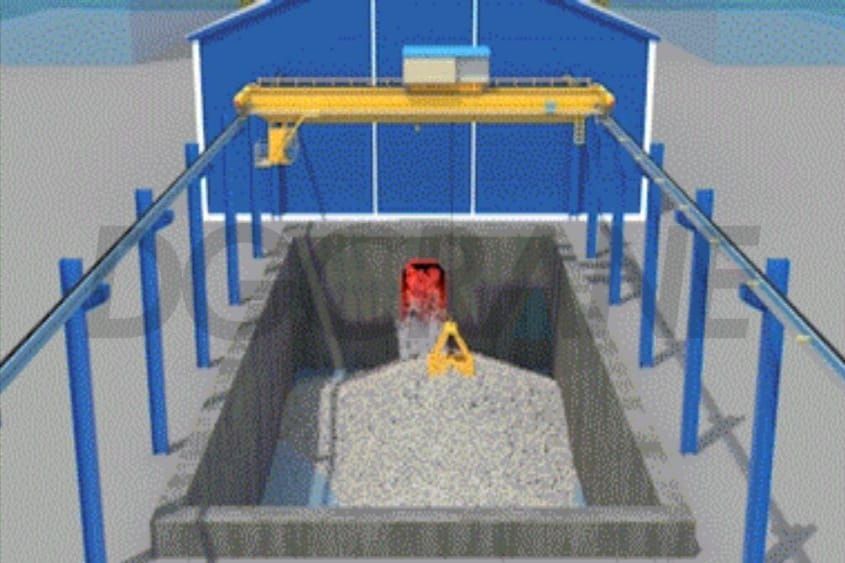
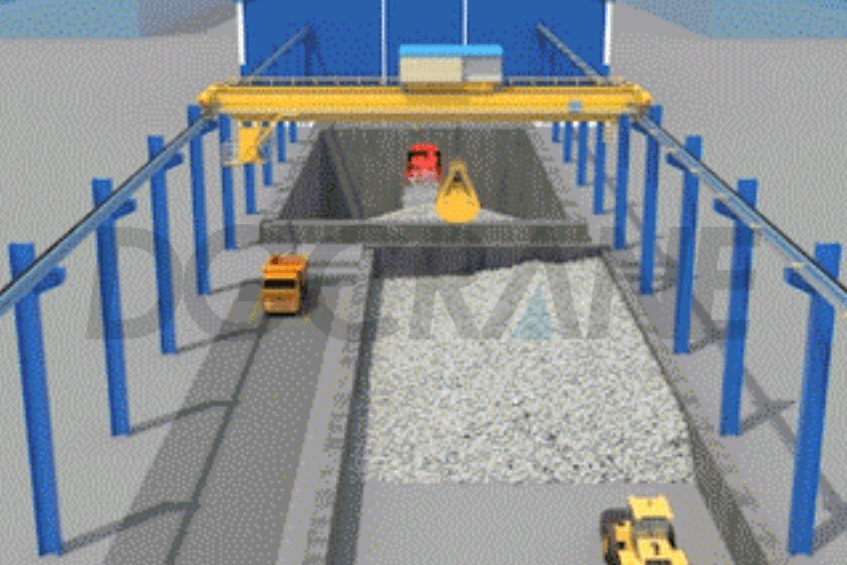
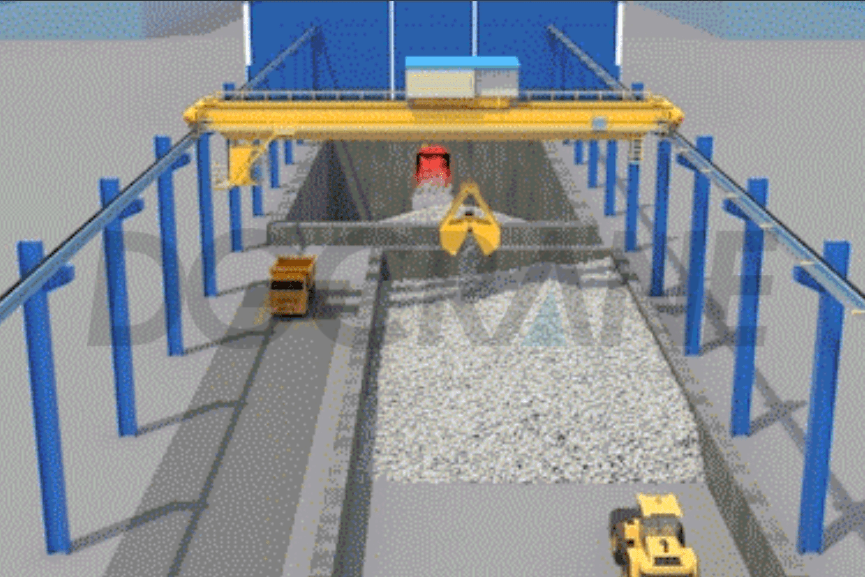
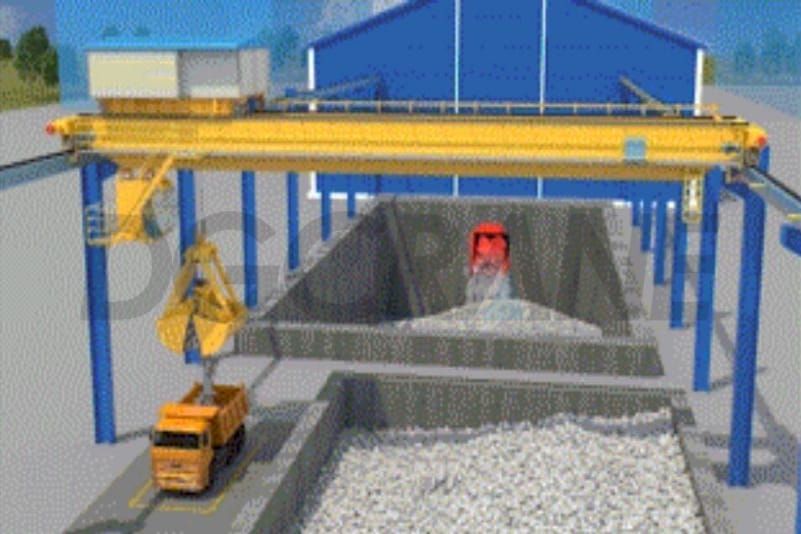
Coker Overhead Crane Price
Our coker cranes are specifically designed to handle the complex working conditions of the refining industry. Each solution is fully customized and optimized based on your project requirements—such as span, lifting height, load capacity, and process environment. Therefore, pricing is calculated according to specific parameters.
With proven technical expertise and extensive global project experience, we are committed to providing highly reliable, long-lifespan equipment along with full lifecycle service support. For an accurate quote or solution consultation, feel free to contact our professional team at any time. We'll respond promptly and tailor a cost-effective solution to meet your exact needs!
Coker Overhead Crane Case
The enclosed unmanned coke removal crane system in this petrochemical project is equipped with two 20 ton explosion-proof bridge cranes, each with a span of 31.5 meters and a rail elevation of 18 meters. The system features intelligent obstacle avoidance and precise control, ensuring high operational safety while enabling automatic high-intensity operation.
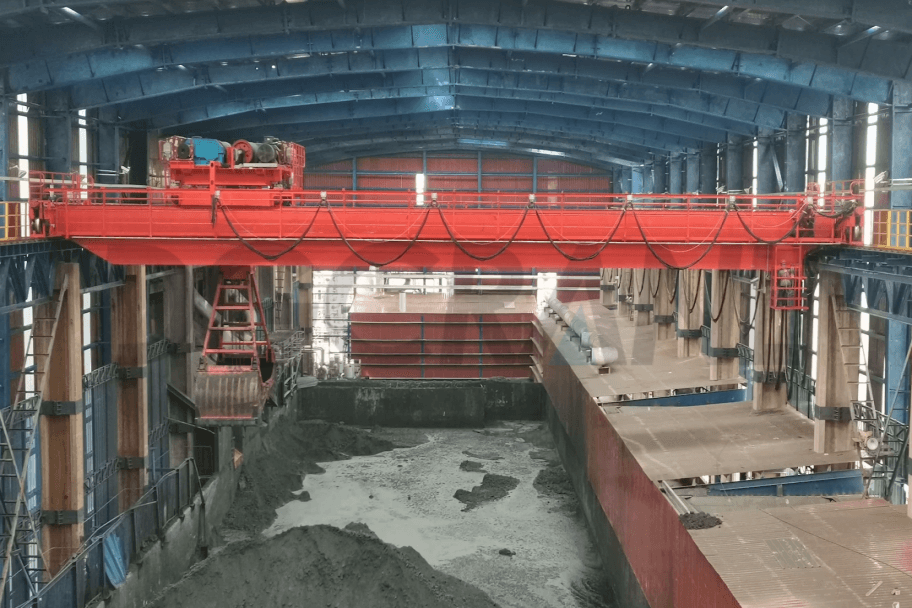
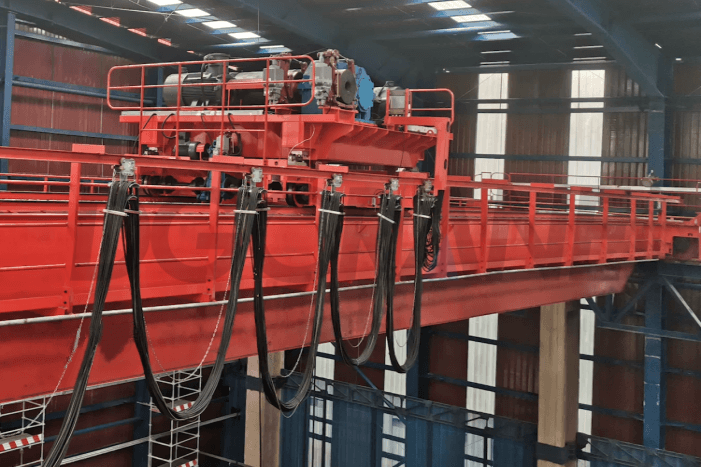
The intelligent crane management system in this project includes a scheduling module that automatically generates feeding, discharging, and material transfer tasks based on optimal efficiency principles. The cycle time per operation has been reduced to under 2 minutes, significantly boosting crane operational efficiency. Additionally, the system innovatively adopts an ultra-frequency control method for the grab bucket’s opening and closing, increasing the bucket fill rate to over 90% and saving at least 8 seconds per work cycle.
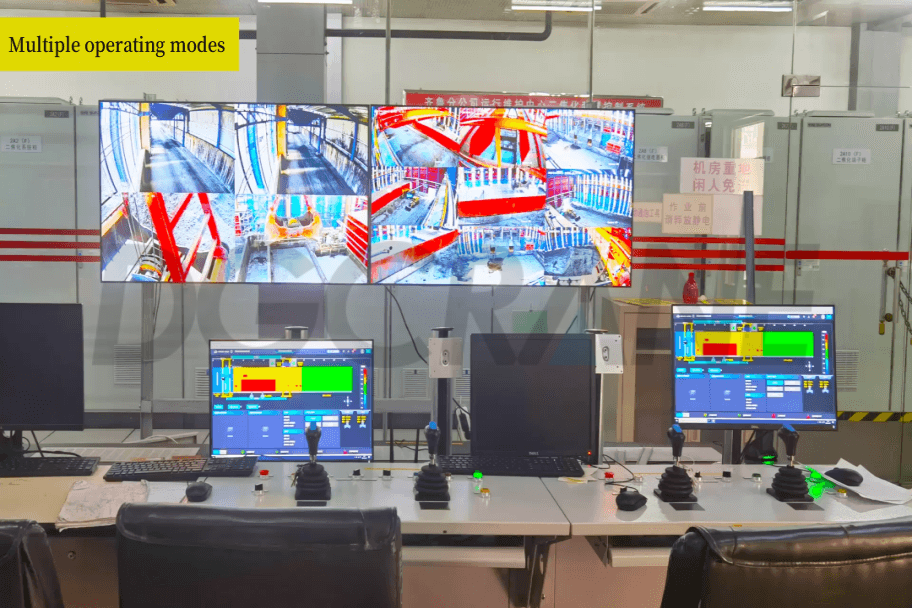
The central control room of this petrochemical project is equipped with an intelligent remote control console, integrated with the crane operation panel and the intelligent crane management system. This setup enables system mode switching, equipment monitoring, fault warning, and remote operation. The system supports four interchangeable operating modes: fully automatic, semi-automatic, remote manual, and on-site remote control. This flexibility allows not only for routine automated operations but also for handling various special tasks as needed.
Multiple cameras are installed at key positions on the cranes and throughout the facility, enabling 360-degree real-time surveillance of the yard with no blind spots. This robust monitoring system effectively supports remote crane operation for the client.
Other Types of Coker Crane
The coker crane features a versatile structural design that can be tailored to suit different coke pit layouts. It supports multiple configurations, including overhead cranes (EOT), single-leg gantry cranes, and gantry cranes. This flexibility ensures optimal adaptability to a wide range of site conditions and operational requirements.
Single Leg Coker Gantry Crane
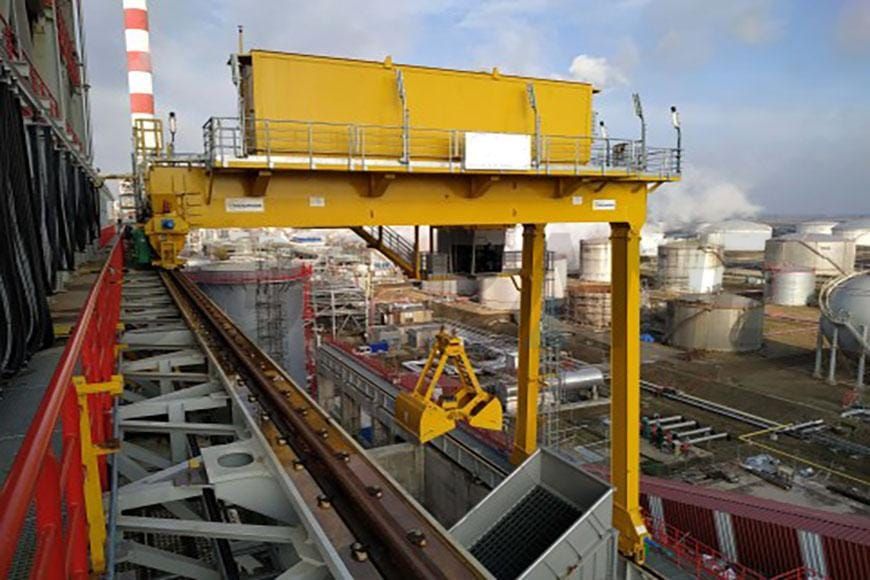
Structural Features:
Only one side of the crane is equipped with supporting legs that run along a ground rail, while the other side relies on the existing support structure of the plant building.
Applicable Scenarios:
- Workshops, warehouses, or open areas with limited space, especially where one side has an available building structure for support;
- Lifting of small to medium-sized equipment and material transfer along production lines, offering a balance of flexibility and space efficiency;
- Offers better stability and cost-effectiveness compared to gantry cranes.
Coker Gantry Crane
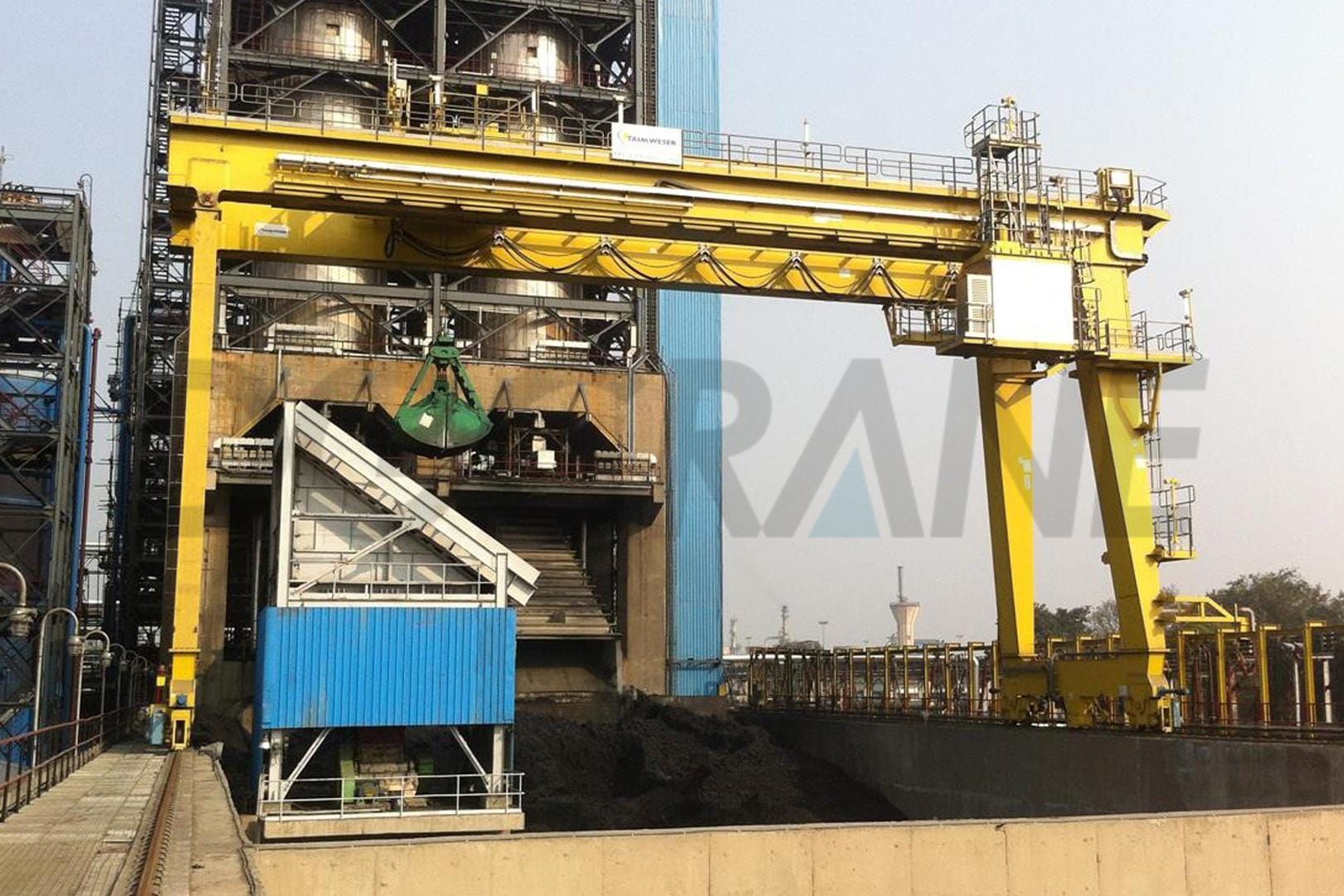
Structural Features:
Equipped with independent supporting legs on both sides, requiring two ground rails to form a “gantry”-shaped framework.
Applicable Scenarios:
- Open outdoor areas such as coking plants, railway freight yards, and open stockyards;
- Long-distance lifting operations without the need for overhead rail support structures;
- Industrial settings requiring high load capacity, high efficiency, and large spans.
Coker Crane FAQ
What is the main function of a coker crane?
A coker crane is used in coking units to handle newly produced high-temperature coke, transferring it to the coke pit for cooling. After cooling, the crane moves the coke to the crusher, hopper, or conveyor system.
What intelligent features does a coker crane have?
Modern coker cranes are equipped with intelligent control systems, such as synchronized grab bucket hoisting to maintain even tension on the wire ropes. Additionally, anti-skewing control reduces wear on wheels and rails, while anti-sway control minimizes load swing, enhancing operational safety and efficiency.
What are the environmental challenges for operating a coker crane?
These cranes operate continuously in harsh environments characterized by high temperatures, high humidity, corrosive gases, and abrasive dust. These conditions demand higher standards in crane design, material selection, and maintenance strategies.